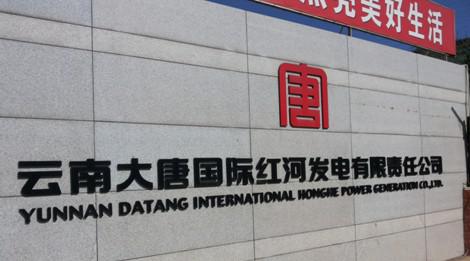
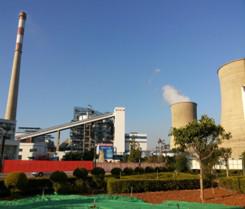
Second, the frequency conversion project situation Yunnan Datang Honghe Power Plant 1 #, 2 # units each with two primary fans (6kv, 3600kw) and two secondary fans (6kv, 2240kw) in 2009 successfully used the Beijing Leader Huafu Electric Technology Co., Ltd. high voltage inverter. Since it was put into operation so far, the equipment has been operating stably and there have been no abnormal shutdowns.
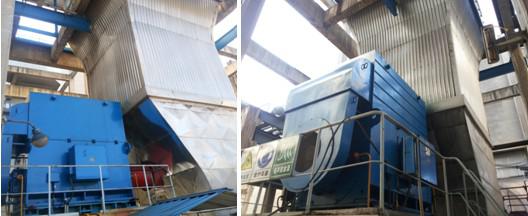
Third, on-site equipment parameters 1 #, 2 # unit 4 fan supporting motor parameters: voltage 6kv, current 346A, power 3000KW.
1#, 2# unit 4 secondary fan supporting motor parameters: voltage 6kv, current 257A, power 2240KW.
High-voltage inverter model: one: HARSVERT-A06/440 (3600KW), second: HARVVERT-A06/270 (2240KW).
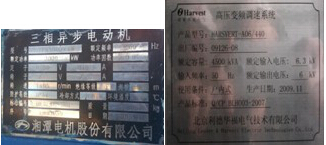
Fourth, the primary circuit design once, the secondary fan frequency conversion velocity modulation system uses the manual tow a plan, the basic principle is as follows:
• Composed of 3 high-voltage disconnecting switches QS41, QS42 and QS43 and high-voltage switch QF, motor M (see the left figure).
• There is a mechanical interlock logic between QS42 and QS43 that cannot be closed at the same time. In frequency conversion operation, QS43 is disconnected and QS41 and QS42 are closed. When power frequency is running, QS41 and QS42 are disconnected and QS43 is closed.
• The high-voltage switch QF and motor M are the original equipment on site.
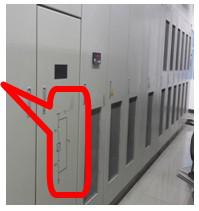
V. High-voltage inverter installation diagram
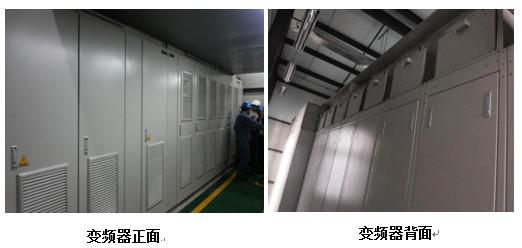
VI. Heat Dissipation Scheme The project uses an empty water cooling scheme. The hot air of the frequency converter is applied to the air-cooling device through the air duct for heat exchange, and the cooling water directly takes away the heat generated by the frequency converter; the cooled cold air is circulated back to the room through cooling.
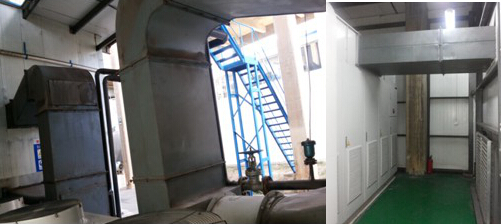
The temperature of the inlet cold water in the air-cooling device is lower than 33°C, which can fully ensure that the hot air passes through the heat sink and the ambient temperature of the inverter is controlled below 40°C to meet the environmental requirements of the inverter. The air-water cooling system completely separates the cooling water from the circulating air. The water pipeline is clearly separated from the high-voltage equipment outside the frequency conversion room, and the system itself is provided with a ventilation and opening conversion method to ensure that the air-water cooling system does not cause problems in the operation of the entire inverter system. Security threats and accidents. At the same time, as the room is closed, the inverter uses the indoor circulating air to cool the equipment, which has the characteristics of low dustiness and low maintenance, and reduces the adverse effect of the environment on the stability of the inverter.
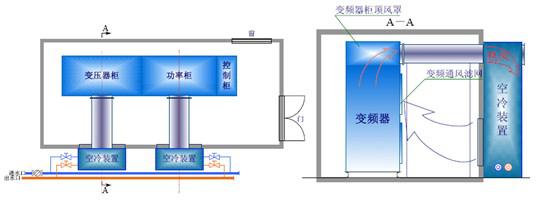

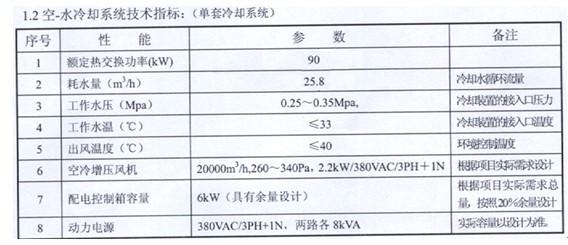
Seventh, DCS control system The frequency changer control all realizes above the central control room DCS. Including inverter frequency setting, start, stop, emergency stop, fault alarm and other signals.
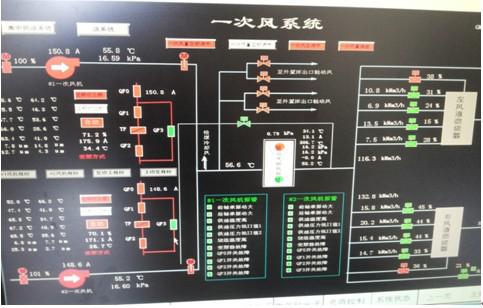
The communication between the inverter and the DCS adopts a hard-wired connection, which has convenient wiring and good stability.
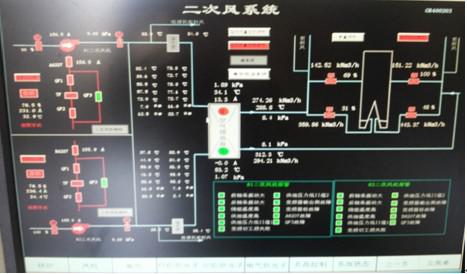
VIII. Power Saving Effect Since the operation of four primary and four secondary fan inverters has been put into operation, the operating frequency is not fixed due to load fluctuations in the first few months. From 2010 to now, it has been running between 35Hz and 40Hz. This frequency band can fully meet the production needs.
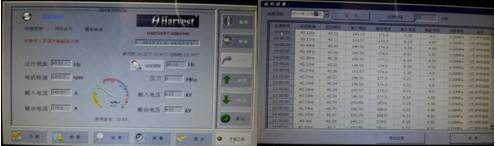
User statistics of No. 1 boiler power frequency and frequency conversion power consumption comparison chart.
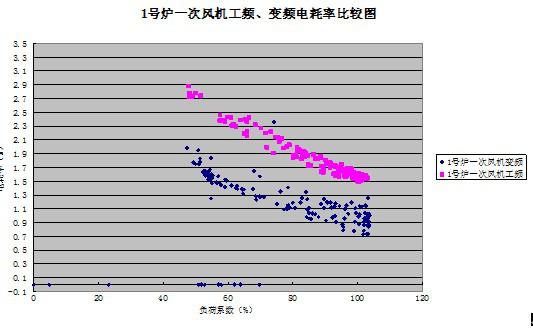
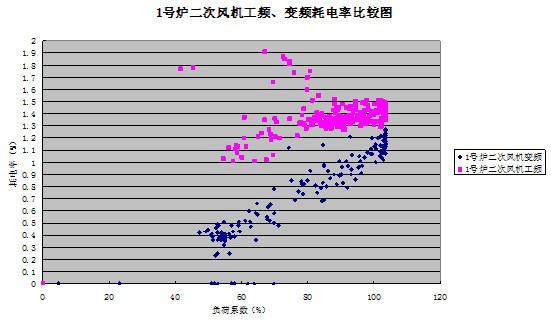
According to the statistics and records of users, the average annual electricity saving rate of 4 primary fans is analyzed as follows (average load is 80%, annual operation is 7200 hours):
The annual power consumption of 4 primary fans at the power frequency is about 300,000 x 0.8 x 0.0085 x 7200 = 1,468,8000 degrees. The annual power consumption of each of the 4 primary fan inverters is approximately: 300,000 x 0.8 x 0 .0064x7200=11059200 degrees 4 primary fans each annual electricity savings = 3628800
Annual saving rate of 4 primary fans per year: 3628800/14688000=24.7%
According to the statistics and records of users, the annual average energy-saving rate of 4 secondary fans is analyzed as follows (average load is 80%, annual operation is 7200 hours):
The annual power consumption of each of the four secondary fans at the power frequency is approximately 300,000 x 0.8 x 0.0083 x 7,200 = 14,342,400 degrees. The annual power consumption of each of the 4 secondary fans in the frequency conversion is approximately: 300,000 x 0 .8x0.006x7200=10368000 degrees 4 sets of secondary fans each annual electricity savings = 3974400
Annual energy saving rate of 4 secondary air fans per year: 3974400/14342400=27.7%
Tungsten Trioxide,Blue Tungsten Trioxide Msds,Mercury Blue Tungsten Trioxide,Yellow Crystalline Powder
HUNAN ZHONGNAN ANTIMONY&TUNGSTEN TRADING CO.,LTD , https://www.zhongnanats.com